Diluting glacial acetic acid is a critical process, especially in industries like pharmaceuticals, food production, and chemical manufacturing. As one of the purest forms of acetic acid,
glacial acetic acid has a concentration of 99.5% or higher. Handling and diluting it requires expertise due to its corrosive nature and potential to cause harm if mishandled.
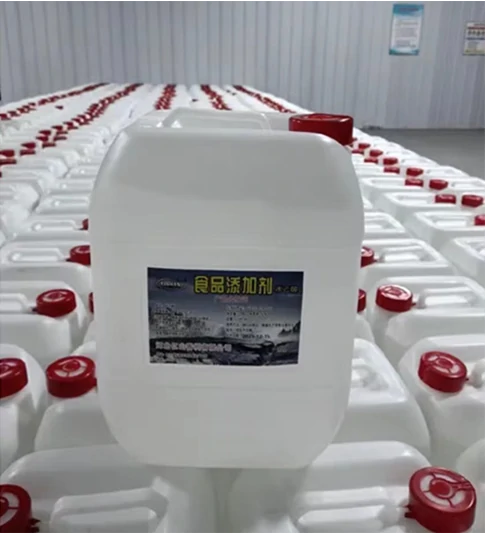
Expert practitioners understand that the first step in diluting glacial acetic acid is selecting the right water quality. Deionized or distilled water is preferred over tap water to avoid unintended chemical reactions that might occur with minerals and impurities found in tap water. Using high-purity water ensures that the resulting diluted acetic acid maintains its integrity for usage in sensitive applications.
Preparing the workspace with proper safety equipment, including gloves, goggles, and lab coats, is crucial. Given that glacial acetic acid can cause severe burns upon contact with skin, using personal protective equipment is non-negotiable. Additionally, a fume hood is recommended to avoid inhaling acetic acid vapors, which can cause respiratory distress.
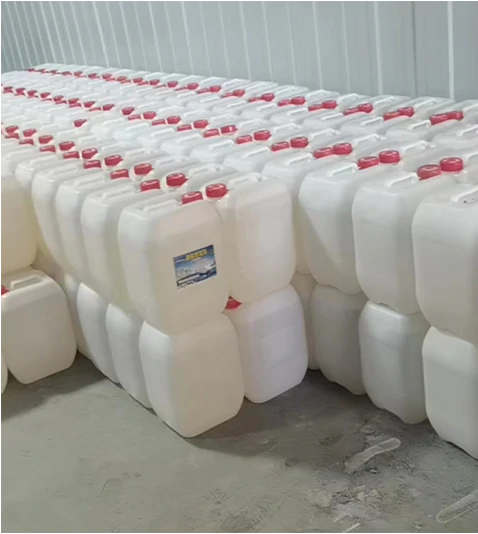
For those well-versed in handling chemicals, the process of dilution is straightforward but demands precision. Begin by measuring the desired volume of water in a suitable container, preferably glass or high-density polyethylene, to prevent any reaction with the container material. The rule here is always to add acid to water, not the reverse. This approach reduces the risk of an exothermic reaction that can lead to splattering, particularly with glacial acetic acid's high concentration.
Professionals recommend adding the glacial acetic acid slowly to the water while stirring constantly. This technique ensures that the acid disperses throughout the water evenly, minimizing localized concentrations of heat. Stirring also helps in balancing the temperature of the solution, further contributing to safety.
diluting glacial acetic acid
For industries producing large quantities, automated systems are ideally used. These systems employ precise controls to monitor temperature and concentration, significantly reducing labor costs and potential human error. The integration of these systems is an investment but justifiable by the increased safety and efficiency they bring.
Experts highlight the importance of calibration and verification in dilution processes. Regularly calibrated equipment ensures that the desired concentration is achieved accurately, which is critical for maintaining product quality and compliance with industry standards. The location of dilution, ambient temperature, and materials used also play key roles. Variations here can result in slight changes in concentration, which might be impactful in highly regulated environments.
Trustworthiness is established through proper documentation of the dilution process and adherence to standard operating procedures. Transparent reporting builds confidence, especially in sectors where traceability and accountability are paramount. Digital solutions that record each step in real-time are preferred as they allow for easy storage and retrieval of records for audits or reviews.
In conclusion, while diluting glacial acetic acid may seem a simple task, it encapsulates a mix of experience, expertise, authority, and trustworthiness. Handling such a potent substance demands rigorous adherence to safety protocols, precision in execution, and a deep understanding of the chemical properties and potential implications. By prioritizing these factors, industries can safely and effectively utilize glacial acetic acid, ensuring product efficacy and safety.