Glacial acetic acid, a colorless liquid with a pungent smell, is a highly concentrated form of acetic acid and a vital chemical in various industrial applications. While its usefulness is undeniable,
handling glacial acetic acid requires strict adherence to safety precautions. Understanding the risks and implementing preventative measures is crucial to maintaining a safe environment for workers and ensuring product integrity.
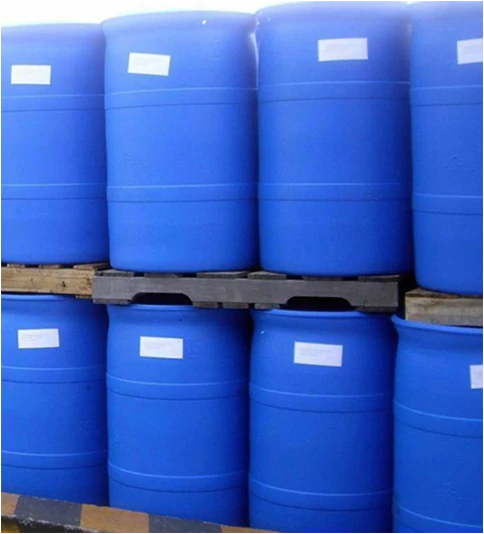
One of the key aspects of working safely with glacial acetic acid involves thorough knowledge of its properties. It is a corrosive substance capable of causing severe burns upon contact with skin or eyes and is harmful if inhaled or ingested. Therefore, obtaining proper training on handling and emergency procedures is critical for anyone expected to work with this chemical. Training programs should encompass not only theoretical aspects but also practical drills to reinforce safety protocols.
Appropriate personal protective equipment (PPE) is non-negotiable when dealing with glacial acetic acid. Suitable PPE includes chemical-resistant gloves, safety goggles, face shields, and lab coats or aprons designed to resist acid penetration. Respiratory protection may also be necessary in situations where ventilation is insufficient or during spill cleanup operations. Employers must ensure that high-quality PPE is readily available and well-maintained.
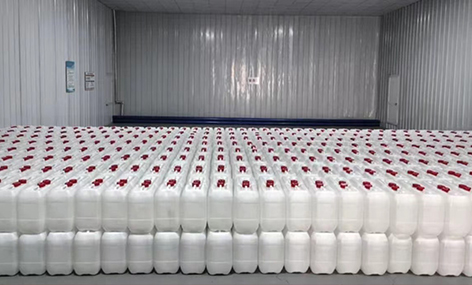
Implementing adequate ventilation systems is another cornerstone of safely handling glacial acetic acid. Fume hoods or local exhaust ventilation should be employed to capture and neutralize fumes at their source, minimizing the risk of inhalation exposure. Regular maintenance of these systems is essential to ensure their effectiveness and to prevent any potential malfunctions.
Storage considerations play an equally important role in the safe handling of glacial acetic acid. It should be stored in a cool, well-ventilated area away from incompatible substances, such as strong oxidizers and bases, which could trigger dangerous chemical reactions. Containers must be clearly labeled and constructed from materials resistant to acetic acid corrosion, such as glass or certain plastics. Moreover, secondary containment measures, like spill trays, can prevent the spread of leaks and spills, mitigating potential hazards.
glacial acetic acid safety precautions
In terms of emergency preparedness, every facility using glacial acetic acid should have an actionable plan in place. This includes easy access to eyewash stations and safety showers, fire extinguishers for chemical fires, and first-aid supplies. Emergency contact numbers and Material Safety Data Sheets (MSDS) should be prominently posted and easily accessible. Workers must be acquainted with these resources and trained on their use to respond swiftly and effectively to accidents or exposures.
Continuous monitoring of work environments where glacial acetic acid is used is essential to ensure exposure levels remain within safe limits. This can be achieved through regular air quality assessments and personal exposure monitoring. Should thresholds be exceeded, immediate action must be taken to rectify unsafe conditions. Employers must also foster a culture of safety by encouraging workers to report any concerns or incidents without fear of retaliation.
Waste disposal presents another challenge when dealing with glacial acetic acid. Disposal procedures must comply with local, state, and federal regulations to prevent environmental contamination and harm to public health. Neutralization before disposal, typically by diluting and adjusting to a neutral pH, is a common practice. However, it is imperative that these processes are conducted by trained personnel to avoid unintended reactions.
In summary, the safe use of glacial acetic acid relies on a comprehensive approach encompassing education, prevention, and preparedness. By equipping workers with the necessary knowledge and tools, implementing strict safety protocols, and fostering a proactive safety culture, organizations can mitigate risks and ensure both human and environmental safety. Regular reviews and updates to safety procedures will further enhance these efforts, adapting to new insights and technological advancements in chemical safety management.