Glacial acetic acid, known for its pungent smell and versatility, is an anhydrous form of acetic acid that plays a significant role in various industries, including textile, chemical, and food production. The cost of glacial acetic acid, like many chemical commodities, fluctuates based on numerous factors including production costs, demand, and market dynamics. Understanding these elements can facilitate better procurement strategies and cost management for businesses reliant on this chemical.
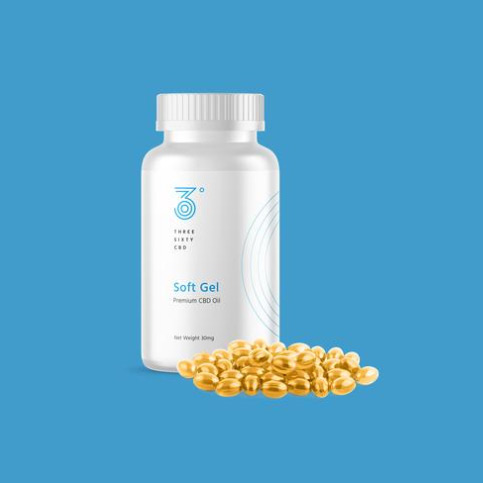
One of the main drivers of glacial acetic acid pricing is the raw material cost, primarily methanol and carbon monoxide, used in its synthesis. Any shift in the prices of these foundational substances can directly affect the market cost of glacial acetic acid. Fluctuations in oil prices can also indirectly influence methanol prices, thereby impacting acetic acid production expenses. Keeping abreast of these variables is crucial for purchasers and manufacturers seeking to hedge against unexpected cost increases.
Additionally, the demand from various industries plays a crucial role in determining the cost of glacial acetic acid. The textile industry, for instance, relies on it for dyeing and finishing processes. As fashion trends evolve or as big players ramp up production, the resulting increase in demand can drive prices upward. Similarly, its use in the production of PTA (purified terephthalic acid) for polyester manufacturing heavily influences its market valuation. Increased demand from developing markets or a boom in polyester production can lead to significant price variations.
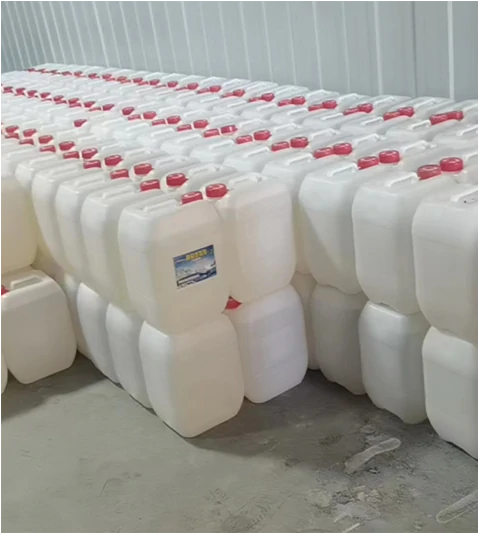
Environmental policies and regulatory changes also impact the cost of glacial acetic acid. Stricter environmental regulations can alter production costs due to the need for upgraded equipment or processes that comply with new standards. Such regulatory shifts often lead to either temporary shortages or increased production costs, subsequently affecting the market price.
Logistics and supply chain factors cannot be overlooked when considering the cost of glacial acetic acid. Transporting chemical products safely and efficiently requires specific conditions, including temperature control and specialized containers. Variations in logistical costs can therefore directly impact end prices. Global events, such as geopolitical tensions or natural disasters, can disrupt supply chains, causing delays and increasing transportation costs. Businesses must proactively manage these risks by diversifying their supplier base and maintaining strategic inventory levels.
glacial acetic acid cost
The competitive landscape among manufacturers can also affect the cost of glacial acetic acid. Companies with advanced production technologies or those situated in regions with access to inexpensive raw materials can offer more competitive pricing. Partnerships with such suppliers can provide cost advantages to purchasers. Moreover, technological advancements that increase yield or reduce production time can lower overall costs, emphasizing the importance of innovation in maintaining competitive pricing.
Investing in market research and predictive analytics tools can offer companies a significant edge. By analyzing historical pricing data alongside current market trends, businesses can forecast potential cost increases and adjust their procurement strategies accordingly. Artificial intelligence and machine learning models are increasingly being employed to predict chemical pricing trends, providing purchasers with actionable insights for negotiations and budget planning.
Finally, fostering transparent relationships with suppliers is paramount. Open communication can facilitate better understanding of the factors influencing pricing, thereby aiding more effective negotiations. Trustworthy partnerships ensure that businesses stay informed about potential cost increases or supply issues in advance, allowing them to react promptly.
In conclusion, the cost of glacial acetic acid is influenced by a complex interplay of raw material prices, industrial demand, regulatory changes, logistical factors, and competitive dynamics. To navigate these challenges effectively, businesses should employ a combination of strategic sourcing, market analysis, and supplier relationship management. By doing so, they can achieve cost efficiency and maintain a robust supply chain resilience in the face of market fluctuations. This comprehensive approach not only aids in managing current costs but also positions businesses to adapt to future market developments confidently.