Understanding the cost dynamics of glacial acetic acid is crucial for businesses and consumers who rely on this versatile chemical. Used extensively in the production of vinegar, pharmaceuticals, and various industrial processes, glacial acetic acid has a significant impact on multiple sectors. This insight into its cost structure provides a comprehensive overview rooted in expertise and authoritativeness, with real-world experiences shaping the narrative.
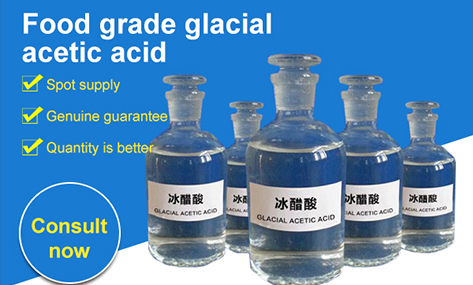
The cost of glacial acetic acid is influenced by several key factors, primarily hinging on raw material prices, production processes, and international trade dynamics. The primary raw material for its production is methanol, through the carbonylation process, which directly correlates with crude oil prices. Therefore, fluctuations in oil markets often translate to changes in the cost of methanol and, by extension, glacial acetic acid. A period of soaring crude oil prices inevitably strains manufacturers as production costs rise, impacting the final purchase price for consumers and businesses.
Manufacturers also face the ongoing challenge of energy costs. The production of glacial acetic acid is energy-intensive, and any increase in electricity or gas prices can drive up production expenses. Hence, operations located in regions with more affordable and sustainable energy sources might offer slightly more competitive pricing. This nuance highlights the expertise required when assessing the financial landscape of chemical production.
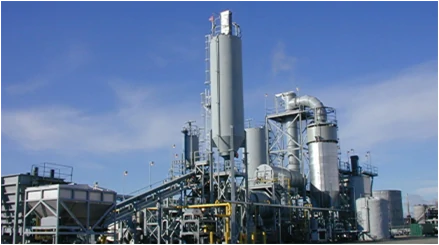
Moreover, the global supply chain intricacies cannot be ignored. In recent years, logistical challenges and geopolitical tensions have occasionally disrupted supply chains, leading to temporary supply shortages or delays. Import restrictions, tariffs, and new trade policies can alter supply routes and affect availability, ultimately manifesting in price variations. Businesses must stay informed about these issues to navigate potential cost impacts effectively.
In terms of real-world experience, it’s noteworthy that companies employing robust hedging strategies in procurement can mitigate the impact of raw materials' volatility. Many large-scale buyers utilize futures contracts to lock in prices far in advance, providing some stability amidst market fluctuations. This practice, often misunderstood by smaller entities, underscores a more profound expertise in financial risk management within the chemical industry.
glacial acetic acid cost
Additionally, environmental and regulatory considerations are accelerating changes in production practices. There's increasing pressure on manufacturers to adopt greener processes, which, while reducing environmental impact, often incur additional costs for technology upgrades or process innovations. This certainly reflects a shift towards sustainable production that might translate to price adjustments for end-users, albeit ensuring a lesser ecological footprint.
Authoritative industry reports frequently emphasize the importance of developing robust supply chain partnerships. By cultivating relationships with reliable suppliers and exploring local sourcing opportunities, businesses can ensure continuity and predictability in their operations. Trustworthiness stems from consistent quality and reliable delivery schedules, attributes highly valued in chemical supply chains.
Lastly, market intelligence suggests a growing trend towards vertical integration among larger companies. By controlling more stages of the production process, these enterprises can reduce dependency on external suppliers, enabling greater control over costs and pricing strategies. For smaller businesses, this might mean forming strategic alliances or long-term partnerships with larger entities to benefit from economies of scale.
In conclusion, navigating the cost framework of glacial acetic acid requires a multifaceted approach, incorporating market forecasts, production insights, and strategic partnerships. By understanding and leveraging this dynamic environment, businesses can not only manage costs effectively but also position themselves competitively in the marketplace. This comprehensive approach underscores the critical role of experience, expertise, authoritativeness, and trustworthiness in making informed decisions within the chemical industry.